A new water-splitting technique to generate clean hydrogen

Electrolytic hydrogen production entails the generation of hydrogen from water using electrical power, which should ideally come from renewable power sources such as sunlight and wind. Although this method of producing hydrogen could be a very promising solution for increasing sustainability, but researchers will have to overcome several key challenges in order for it to become widespread.
In a recent study featured in Nature Energy, a team of researchers at the Technion-Israel Institute of Technology have addressed some of these challenges, presenting a new technique for splitting water that could enhance existing electrolytic hydrogen production methods. Their research draws inspiration from one of their previous studies on photoelectrochemical (PEC) water splitting, in which they tried to combine solar energy and water (photo)electrolysis to generate hydrogen from sunlight and water.
One of the greatest challenges outlined in this previous work was the collection of hydrogen gas from millions of PEC cells distributed in the solar field. In their study, the Technion-based researchers tried to develop a technique that could effectively tackle this challenge.
“Taking photovoltaic (PV) solar plants as the base scenario, the solar farm is composed of millions of individual PV cells, where the current (and voltage) is collected from each and every one of them into a metal grid,” Avner Rothschild, one of the researchers who carried out the study, told TechXplore. “This is easy with electricity, but not so with hydrogen gas.”
In an ideal PEC solar plant of the future, PV cells would be replaced by PEC cells, which can produce hydrogen in a component known as cathode compartment, and oxygen in a separate chamber called an anode compartment. These two compartments should be separated, at the very least by a membrane, in order to ensure that hydrogen and oxygen do not mix, as this would cause an explosion. In addition, the hydrogen gas must be collected from each individual cell.
Creating this setup has so far proved to be technically difficult and expensive, as it requires a very costly piping manifold. Ultimately, this has made the realization of solutions for large-scale hydrogen production by PEC water splitting unrealistic.
“We sought a way out of this challenge, and came up with the idea of separating the oxygen and hydrogen compartments in the PEC cell into two separate cells, so that the oxygen is generated in the solar field and is released to the atmosphere, whereas the hydrogen is generated in a central reactor at the corner of the field,” Rothschild said. “The separation into two cells is made possible by inserting another set of two electrodes, called auxiliary electrodes, that are being charged and discharged simultaneously by OH– ions involved in the water-splitting reaction, thereby mediating the ion exchange between the two cells (which is necessary to close the electric circuit).”
In their previous paper, published in Nature Materials, Rothschild and his colleagues presented a disruptive new approach for water electrolysis (electrolyzers) and photoelectrolysis (PEC) architectures. This promising approach, however, introduced another challenge of regenerating the auxiliary electrodes when they get saturated at the end of a production cycle. The researchers suggested that the electrodes could be swapped at the end of each cycle, but this would be rather cumbersome, so they continued exploring alternative solutions.
“We then discovered that when you heat the auxiliary electrode in the hydrogen cell, after it was charged (to become NiOOH), it releases oxygen gas bubbles spontaneously and regenerates to its initial state (Ni(OH)2),” Rothschild said. “This discovery led to the development of the E-TAC water-splitting process that is presented in the present work.”
E-TAC, the new water-splitting technique proposed by Rothschild and his colleagues, has a high energy efficiency of 98.7 percent, hence it significantly outperforms conventional electrolyzers, which typically have an energy efficiency of ~70 to 80 percent for state-of-the-art devices. A further advantage of E-TAC is that it produces hydrogen and oxygen sequentially, while in most other electrolyzers, they are produced simultaneously. This ultimately removes the need for a membrane separating the hydrogen and oxygen gases, thus greatly simplifying the construction and assembly of the cells, as well as their operation and maintenance.
“Potentially, this could translate into big savings on capital and operation costs, leading to the development of cost-effective water-splitting technology that may compete with SMR (steam methane reforming), offering cheap hydrogen with no CO2 emissions, provided that the electricity comes from renewable sources such as hydropower, solar or wind power,” Rothschild said.
In conventional water electrolysis, hydrogen and oxygen are always produced simultaneously in the cathode and anode compartments, respectively. The compartments are placed as close as possible to one another, to minimize electrical Ohmic losses, and they are separated by a membrane to avoid the creation of an explosive H2/O2 mixture.
“The cathode reduces water, generating hydrogen (H2 molecules) and hydroxide ions (OH–) through a reaction known as HER (hydrogen evolution reaction),” Rothschild said. “The OH– ions migrate to the anode through the electrolyte and through the membrane, where they are oxidized through the OER (oxygen evolution reaction). Together, these two reactions (HER and OER) complete the water splitting reaction: 2H2O 2H2 + O2.”
In conventional water electrolysis, the two electrochemical reactions described by Rothschild are coupled in both time and space, as they occur simultaneously, in the same cell and at close proximity. Moreover, these characteristics are the same whether the process is applied to alkaline or PEM electrolyzers.
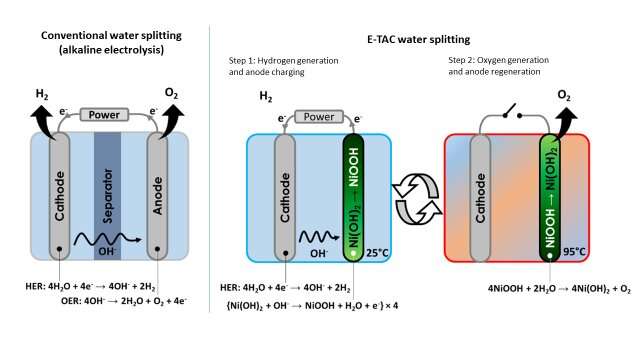
Unlike this traditional approach to water electrolysis, the water-splitting process devised by the researchers decouples the HER and OER reactions, which instead occur at different times and potentially in different parts of a device. Rather than being continuous, therefore, E-TAC can be described as a ‘batch process’ with two cycles, the first generating hydrogen electrochemically and the second oxygen via a spontaneous chemical reaction.
“We place the cathode (the same cathode used in alkaline electrolysis) and the anode (which is different from the anode in conventional electrolysis) in an electrolytic cell and pass current between them,” Rothschild said. “The cathode generates hydrogen through the HER reaction, just like it does in the conventional water electrolysis case, but the anode does a completely different thing. The anode essentially gets charged by absorbing the OH– ions that are generated at the cathode, and gradually transform from Ni(OH)2 (nickel hydroxide) to NiOOH (nickel oxyhydroxide).”
Interestingly, the reaction produced in the anode is the same one that occurs at the cathode of alkaline batteries (e.g. Ni-MH batteries) while they are charging. This suggests that it can work well for many cycles, just as it does in alkaline batteries.
Sometimes, however, the charging of the anode in the E-TAC process needs to be interrupted, because if it gets overcharged, it could start generating oxygen. When the charge goes above a certain level, therefore, the researchers need to limit the voltage applied to the cells to avoid possible explosions derived from the co-generation of oxygen and hydrogen.
“In order to continue the E-TAC process, we then need to regenerate the charged anode (NiOOH) back to its initial state (Ni(OH)2),” Rothschild explained. “We do so by raising its temperature, thereby accelerating the rate of the spontaneous chemical reaction between the charged anode and water, which releases oxygen and regenerates the anode back to its initial state.”
The technique devised by Rothschild and his colleagues thus entails the use of heat to control the chemical reaction that generates oxygen, as the rate of the reaction slows down at low temperatures and accelerates at high temperatures. The generation of hydrogen occurs at a low or ambient temperature, and the generation of oxygen at high temperatures around 95 degrees Celsius. This is why the researchers decided to call it the E-TAC process, which stands for electrochemical-thermally activated chemical process.
“In the proof-of-concept lab tests presented in our article, we manually moved the anode from the cold cell (i.e. a glass beaker filled with alkaline aqueous solution at ambient temperature) to the hot cell (i.e. the same type of beaker, but heated to 95 degrees Celsius), so the separation between hydrogen and oxygen generation was not only in time but also in place,” Rothschild explained. “However, in a real-world industrial system, we foresee a different scenario in which the two electrodes (anode and cathode) and stationary (not moving), whereas the cell in which they are is filled sequentially with cold or hot electrolyte solutions.”
Separating the production of hydrogen and oxygen, which removes the need for a membrane separating the two different chambers inside electrolytic cells, results in substantial savings over traditional electrolysis approaches. In fact, sealing the membrane is generally expensive and also complicates the overall production process. The membrane in conventional systems requires high-purity water and ongoing maintenance, all of which are unnecessary in E-TAC.
In addition, the technique devised by Rothschild and his colleagues entirely eliminates the risk of volatile encounters between oxygen and hydrogen, as well as resulting explosions. In traditional systems, on the other hand, this risk is still present, as the membrane could rip or its seal could break.
“Currently, the use of membranes also limits the pressure in hydrogen production,” Rothschild said. “E-TAC renders the membrane unnecessary, thus facilitating hydrogen production under much higher pressure and eliminating some of the high costs of compressing the hydrogen later. Moreover, in the new process we proposed, oxygen is produced via a spontaneous chemical reaction between the charged anode and the water, without using an electrical current. This reaction eliminates the need for electricity during oxygen production and increases energetic efficiency from ~70 to 80 percent using customary methods to an unprecedented 98.7 percent.”
The technique developed by Rothschild and his colleagues could lower operating costs of sustainable hydrogen production and equipment costs. The researchers have estimated that the production costs for equipment based on E-TAC would be approximately half of those for existing technologies.
“The process we invented presents a conceptual breakthrough in water splitting, and in view of the advantages it offers, it may become a game-changer and lead to a new technology for hydrogen production from water without CO2 emissions, which could compete with SMR to produce clean hydrogen and enable the transition from fossil fuels to clean hydrogen fuel,” Rothschild said.
After they finished writing their paper, the researchers at Technion patented their invention and founded a start-up called H2Pro, with the mission of developing and distributing new water splitting technology based on the E-TAC technique. They hope to soon commercialize this technology by scaling-up the electrodes and cells used in their study, constructing and testing hydrogen generators based on the E-TAC water-splitting process, optimizing their operation scheme and examining high-pressure hydrogen production.
“We also plan to carry out further academic research to study new electrode materials and apply advanced analytical methods to understand the correlations between electrode composition and microstructure and its function properties, in order to develop the next generation of Ni(OH)2-based electrodes for our E-TAC water-splitting process,” Rothschild said. “Our goal is to improve their capacity (so that we can run longer processes) with fast charging and regeneration rates to enable high hydrogen production rates.”